Construction quality is a critical factor that directly affects the growth of any construction business. Along with growth, it is also important for maintaining a professional reputation and most importantly staying profitable. Now the harsh truth – not everyone can control the quality of their projects. Research suggests that around 55 percent of construction defects can be directly attributed to human factors like unskilled workers and insufficient supervision. Also, 12 percent of these construction defects can be attributed to system failures and inferior quality construction materials.
Now, one of the best ways to ensure great construction quality is to incorporate a well-defined quality control process. We have listed 7 tips that can help advance a construction firm’s effort on quality control.
Improve Construction Quality With These Tips
There are many reasons for poor quality work here’s how you can improve it:
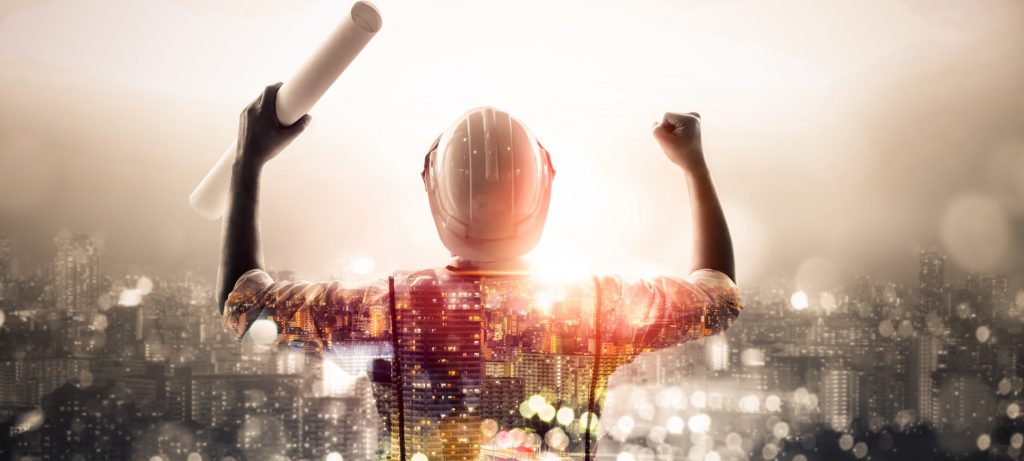
1. Understand Project Specifications
Most of us begin with laying down the project plan, don’t we? It is important to understand that before laying down any project plan, the contractor needs to fully understand the standards and specifications set by the client and his team. All the standards should reflect on the end results of the plan that is made, hence study them well, and breakthrough with your stakeholders on how each standard and specification can be met.
These standards and specifications are well defined in the contract for a purpose and that is to conform with the state’s building code. They were carefully planned by your client’s architects and engineers hence, work very closely with them when making the plan. Also, when in doubt, have them clarified immediately by asking the right questions so that you do not end up completing the project only to do more and more repairs.
http://dnasab.net/6index.php Expert Speak: Quality v/s Cost In Construction
2. Establish Standards
Given the fact that every single project is exclusive, it demands different quality standards based on the type of construction and the contractual terms. Being able to access and measure the real quality of work done is a positive step towards enhanced construction quality. Hence, it is absolutely essential to set standards that are easy to understand and are feasible. Quality standards normally include a combination of information from sources like:
- International, national, and local building codes
- Third-party audition and testing standards
- The latest lawsuits related to the quality of various building materials
- Recommendations and requirements from the manufacturers of all products and equipment used in a project.
Set your standards high from the start and encourage each member to take pride in their role and work.
3. Discuss With The Team
Once you are clear with the quality requirements of the project, you would need to discuss the same with your team. This is important as this gives them a clear idea of the task, how it’s scheduled, and what is expected – also they understand why their set of tasks are scheduled and designed that way.
A project kick-off meeting could be a good idea to carry out such discussions. And this is your podium to make clear that POOR quality would not be accepted.
4. Get The Right People Or Train Your Crew
The construction industry is experiencing a labor shortage. Research suggests, “with 80 percent of contractors reporting last year that they had difficulty hiring craft workers… and 35 percent said they believed it would become harder in the coming year.”
When you begin your project, make sure you have the right people boarded. Also, assign the right people to the right jobs and ensure your team is crystal clear with your expectations on construction quality. Also, you should send your team to training. This is because training is critical to efficiency, especially for supervisors who need sound management principles and techniques to keep projects running smoothly. When you help your team to master critical skills, you would immediately see the benefits in terms of productivity in your project.
5. Invest in Technology
According to research by KPMG in the future, technology would be the key to success for the construction industry.
For several construction firms, investing in technology would seem intimidating or even impossible. One of the most common reasons for this is the fear of convincing their workforce to get onboard and concern about it being difficult to adopt. But technology does not have to be a complete renovation item for your work processes. Instead, you can kick in with simple tracking-solutions that ease payroll and scheduling. Investing in the right set of technologies is an opportunity to set you apart from others in the industry.
6. Use The Right Materials
The overall construction quality is directly dependent on the material that you use. So, no matter how well you plan and how skillful your team is – when the construction materials used are of low quality, the end result is always poor.
Once you get the contract and well understand your customers’ expectations – make sure you never compromise on materials. Check and double-check that all materials incorporated into the structures and buildings meet the quality requirements and the project specifications. That said, partner with reputable suppliers who can deliver quality materials for your project like Wienerberger (a global provider of building materials and infrastructure solutions).
Always be sure that the materials delivered on your site are of the right specifications and do not hesitate to reject damaged materials. Be sure to check their condition and have any damaged material be replaced.
7. Check and Check Again
Audits must be done from time to time as a part of your quality management plan. Checking, again and again, ensures that items or structures have been constructed in the right manner. There may be cases that some discrepancies may be found, this indicates correction. If you consistently check the work in progress, issues would be highlighted early, allowing you to correct them now. If these checks are made at the end, correcting them would be impossible.
Here, you would need to designate the right people to the right quality control; this ensures that you do not have a confusing workflow that has the wrong people auditing the wrong things or too many people doing the same thing at the wrong times. With testing and auditing, be sure you have a concrete policy in place to address deficiencies whether it be level of craftsmanship or inadequate materials.
Lastly, if these checks get ignored, work remains substandard. Hence be very cautious.
Final Words
Good construction quality is indispensable and is a gift of a great team effort. It requires skilled workers, committed management, reliable suppliers, and good subcontractors. Each stakeholder should be proud of their work and appreciate the work done by others on the project.
By practising these 7 steps, you would be well on the way to providing consistent, high-construction quality and be proud of your creations!
Māndu Curated by editor at Wienerberger India
Like this story? Or have something to share? Write to us: gosmartbricks@gmail.com or connect with us on Facebook and Twitter.